
UN0209 производители
In the world of energetic materials, the selection of an explosive compound depends not only on its power but also on its stability, processability, and performance consistency. Among the high-performance compositions used today in military and engineering applications, TR40 Flakes, a blend of 60% RDX (Cyclotrimethylenetrinitramine) and 40% TNT (Trinitrotoluene), stands out for its robust performance characteristics and operational versatility.
This article presents an in-depth exploration of TR40, from its formulation and physical attributes to its advantages, field applications, and handling considerations.
TR40 - Table of Contents:
A Composite Built for Power and Precision
TR40 is classified as a binary high explosive, consisting of two of the most widely used explosive compounds: RDX and TNT. These components are chemically and functionally complementary. RDX, a powerful nitramine explosive, is valued for its exceptional detonation velocity and brisance, while TNT contributes processability, thermal stability, and castability.
The TR40 composition - with a 60/40 RDX-to-TNT ratio - enhances the energy output compared to traditional TNT-based or 60/40 TNT/RDX mixtures like TR60. The reverse ratio ensures that the explosive benefits more significantly from the high detonation performance of RDX, without becoming too sensitive or difficult to manage.
TR40 Flakes: Specification
What TR40 Looks Like and How It Behaves?
TR40 is produced in flake form, which is both practical and performance-enhancing. Flakes offer better flowability and a more uniform packing density during charge assembly. They also reduce the risk of air pockets in cast charges, which can otherwise affect performance and safety.
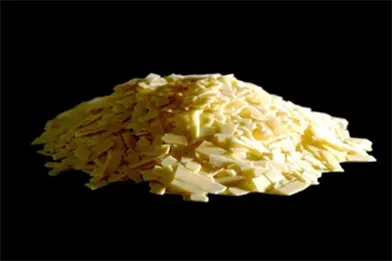
TR40 Flakes.
Visually, the flakes range from yellow to yellowish, with acceptable levels of flake adhesion and the occasional appearance of black spots - both within the normal specification range. The material maintains a low moisture and volatile content (≤ 0.2%), which is critical for preserving stability and preventing degradation during storage or transit.
TR40's detonation velocity, measured at a standard pressed density of 1.6 g/cm³, is ≥ 7,200 m/s - a figure that reflects its high brisance and destructive potential. This velocity ensures that the compound is capable of initiating secondary reactions, penetrating armor, and fragmenting casings with precision.
Another vital performance indicator is the Lead Compression Test result: 25.4 mm, underscoring TR40’s brisance and shock transmission capabilities. Additionally, a Pendulum Power rating of 128% highlights its ability to transfer mechanical energy - a crucial requirement for explosive devices designed for fragmentation or targeted destruction.
Where TR40 Fits in the Explosives Landscape?
Better Than TNT Alone
While TNT is widely known and valued for its handling safety and melt-cast capability, it lacks the energy density and detonation speed needed for modern military applications. TR40 compensates for this with its high RDX content, making it vastly more powerful and efficient in kinetic and blast-based operations.
A Step Beyond TR60 and Hexotol
Compared to TR60 (60% TNT / 40% RDX), TR40 offers a noticeable increase in brisance, penetration ability, and mechanical energy release. This makes it more suitable for applications like shaped charges, armor-piercing warheads, and boosters in large-caliber ammunition.
It can also serve as a performance upgrade over Hexotol, particularly in systems where raw explosive force takes precedence over maximum stability.
Not as Sensitive as Pure RDX
Pure RDX is notoriously sensitive to shock and friction. TR40 mitigates this risk by embedding RDX in a TNT matrix, which tempers its volatility and allows for safer handling. The result is an explosive that approaches the power of pure RDX while remaining practical for mass production, transport, and field deployment.
Applications: From Battlefield to Demolition Site
Thanks to its combination of power, castability, and predictable behavior, TR40 is used in a wide array of settings where precision and impact are non-negotiable.
Military Uses
-
High-Explosive Projectiles: Artillery shells filled with TR40 achieve greater fragmentation efficiency and impact force.
-
Warhead Fillings: Ideal for anti-armor shaped charges and penetration warheads.
-
Grenades and Mines: Used where controlled fragmentation and strong directional energy are required.
-
Booster Charges: Employed as a secondary charge to amplify initiation from detonators to main charges.
Engineering and Demolition
In civil and industrial settings, TR40 is suitable for precision demolition projects. Its high detonation speed and energy transfer make it effective for:
-
Targeted structure removal (bridges, silos, support columns).
-
Controlled blasting in tunneling or mining operations.
-
Demolition of armored or reinforced structures.
Why Flake Form Matters?
The choice of physical form - in this case, flakes - is not just a convenience. It plays a critical role in how the explosive behaves during manufacturing and use.
-
Uniform Distribution: Flakes can be evenly distributed within casings or molds, improving charge consistency.
-
Reduced Air Gaps: Lowers the risk of performance irregularities caused by trapped air.
-
Flowability: Facilitates easier transfer into molds, presses or shell casings.
-
Better Thermal Management: The flake form provides more surface area, aiding heat dissipation during casting.
Material Safety and Handling Guidelines
While TR40 is engineered for controlled sensitivity, it remains a high explosive and demands stringent safety measures. Key handling considerations include:
-
Protective Equipment: Gloves, goggles, and antistatic garments must be used during processing or assembly.
-
Environmental Control: Store in a cool, dry, and well-ventilated area, away from heat, sparks, or open flame.
-
Segregation: Should not be stored with oxidizers, flammables, or incompatible chemicals.
-
Transport: Subject to international dangerous goods regulations (UN Class 1.1D).
Manufacturing environments must be equipped with explosion-proof lighting and ventilation systems, and all staff should be trained in explosive material safety.
Environmental Impact Considerations
As with many traditional high explosives, TNT and RDX carry environmental concerns. Both compounds can persist in soil and groundwater, posing challenges to cleanup and environmental safety, especially in areas of testing, storage, or military activity.
-
TNT Residues: Can break down into toxic byproducts affecting plant and aquatic life.
-
RDX Mobility: Tends to migrate through soil, making it a long-term contaminant if not managed properly.
Efforts to replace traditional formulations with "green" energetics are ongoing, but until then, strict containment and remediation protocols must be followed when using or disposing of TR40.
Equivalent and Related Formulations
TR40 is sometimes referred to under different names depending on organizational or national context. These may include:
-
Cyclotol 60/40: A U.S. military designation for an RDX-rich composite.
-
Enhanced Hexotol: Informally used to describe any TNT/RDX mix exceeding 50% RDX.
-
RDX/TNT Composite 60/40: A general-purpose technical descriptor.
While the chemical formulation remains consistent, these alternate names reflect its adoption across different industries and armed forces.
TR40: Precision, Power and Practicality
TR40 Flakes occupies a critical space in the modern energetic materials landscape. It combines the explosive power of RDX with the handling and casting advantages of TNT, delivering a high-performance product suited for both strategic weapon systems and specialized demolition tasks.
From warheads and booster charges to demolition applications where precision and power must align, TR40 continues to prove its value in both laboratory conditions and real-world deployments.
Its flake form, balanced sensitivity, and technical consistency make it a reliable material of choice where detonation performance is paramount - and where there’s no room for compromise.

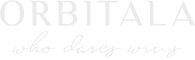
ул. Позитано 9, вх. А, етаж 5, офис 17
София 1000, България
Тел: +359 24434343
WhatsApp: +359-88-596-0050
E-Mail: info@orbitala.eu
